6.5.2 Rollenschälversuch
Abschälung eines dünnen Bleches (flexibles Fügeteil) mit konstantem Biegeradius: Krafteinleitung erfolgt nahezu senkrecht zur Klebefläche
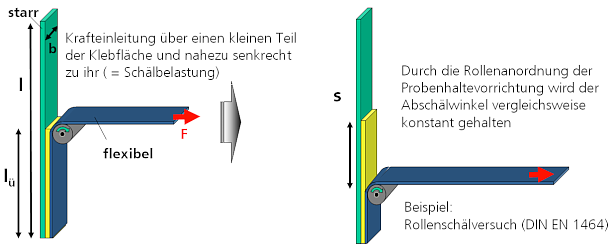
b: Probenbreite (25mm)
l: Probenlänge (> 200mm)
lü: Klebschichtlänge (120mm)
s: Schälweg (> 115mm)
Nur für die Kombination eines starren mit einem flexiblen Fügeteil geeignet
Berechnungsgrundlagen zur Bestimmung des Schälwiderstands:
Schäldiagramm
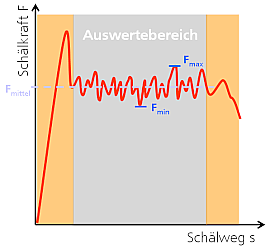
Kraftverlauf im Auswertebereich → mittlere Schälkraft Fmittel
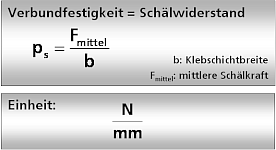
Ferner sind für den Auswertebereich der maximale Schälwiderstand und der minimale Schälwiderstand zu bestimmen (ps,max, ps,min)
Ermittelt wird der Schälwiderstand ps in kN/m (bzw. N/mm) als Durchschnittskraft je Probenbreiteneinheit, gemessen entlang der Klebfuge, die erforderlich ist, um die beiden Fügeteile kontinuierlich voneinander zu trennen.
- Die Probengeometrien für die jeweiligen Methoden sind genormt.
- Zulässige Toleranzen sind festgelegt; Abweichungen von der vorgegebenen Geometrie (z. B. bei Kunststoffen) sind anzugeben.
- Oberflächenvorbehandlung entsprechend den Angaben des Klebstoffherstellers oder der einschlägigen europäischen Norm (z. B. ISO 4588)
- Es sind mindestens fünf Messwerte zu ermitteln.
- Die Proben sind in einem der in ISO 291 festgelegten Normalklimate zu lagern und zu prüfen.
- Die Prüfgeschwindigkeit der Prüfmaschine beträgt z. B. beim Rollenschälversuch 100 mm/min.
- Aufzeichnung der Kraft als Funktion des Weges über den Schälweg; beim Keilspaltversuch wird der Rissfortschritt beurteilt.
Einflüsse auf den Rollenschälversuch
Zur Vergleichbarkeit verschiedener Zugscherversuche müssen die Parameter der Prüfungen bekannt sein und dokumentiert werden.
Dazu zählen in erster Linie:
- Fügeteilmaterial und -geometrie
- Oberflächenbehandlung
- Klebstoff
- Klebstoffschichtdicke
- Aushärtetemperatur und -dauer
- Prüftemperatur
- Prüfgeschwindigkeit
- Bei Haftklebstoffen auch rel. Feuchte
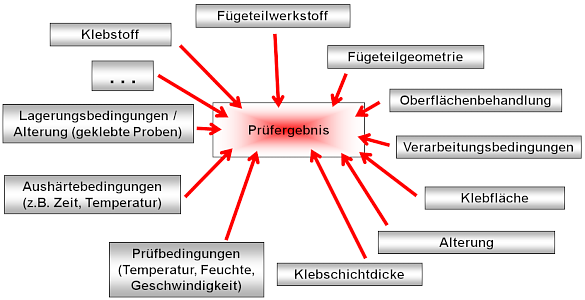