4.5.3 Polymerisation adhesives
Polymerisation adhesives: Cyanoacrylates (superglues)
General description:
- One-component adhesives (1-C)
- Curing initiated by contact with moisture
- Cure to become thermoplastics
Physical properties of the non-cured adhesive:
- Very thin liquids; modified systems: gel-like
Processing properties:
- Manual, semi-automated or fully automated processing
- For preferred equipment contact the adhesive manufacturer
- Processing temperature: room temperature
- Normal contact pressure
- Adhesive film thickness: for very thin liquid products often only up to 0.05 mm: gel-like systems: up to 0.2 mm
- Secure until the bonded joint has reached hand strength
- Take relevant measures for health and safety at work and environmental protection (General: see Section 7; Details: see safety data sheet)
Initiation of the curing:
- Moisture on the surface or air humidity
- Moisture on substrate surfaces
- Contact with basic surfaces, e.g. certain glasses
- Acidic additives or acidic surfaces delay or suppress the curing
- Air humidity (40 – 80 % rel. humidity)
- Hand strength within seconds; final strength after 24 h
- For more than 80 % rel. humidity or highly basic surfaces: risk of shock-curing; leads to reduced strength due to stress in the adhesive film
Typical properties of the cured adhesives:
- Medium to high strength
- Very brittle adhesive, low elongation at fracture
- Temperature for continuous use: up to 80 °C
- Poor resistance to moisture
Points to heed:
- The substrates must be acclimatised prior to bonding, to avoid condensation on the substrate surface that could lead to undesirable shock-curing of the adhesive
- Avoid shock-curing
- Aftercuring: sensitive to moisture and heat
If you have questions about the product then see the technical data sheet or contact the adhesive manufacturer
Polymerisation adhesives: Methyl methacrylate adhesives (MMA adhesives)
General description:
- 2-component adhesive: Resin including accelerator and hardener
- Cure to become thermosets; some cure to become thermoplastics
Physical properties of the non-cured adhesives:
- Consistency: Liquid to paste-like
Processing properties:
- Manual, semi-automated or fully automated processing
- For preferred equipment contact the adhesive manufacturer
- Processing temperature: Room temperature
- Normal contact pressure
- Adhesive film thickness: varied depending on the processing method:A/B method: 0.2 – 0.4 mm, No-mix method: 0.15 – 0.25 mm
- Processing methods:A/B method, no-mix method, conventional 2-C processing: twin cartridges, direct hardener addition
- Hand strength reached after a few minutes; final strength after several hours
- Heat input during curing not necessary
- Secure until the bonded joint has reached final strength
- Take relevant measures for health and safety at work and environmental protection (General: see Section 7; Details: see safety data sheet)
A/B method
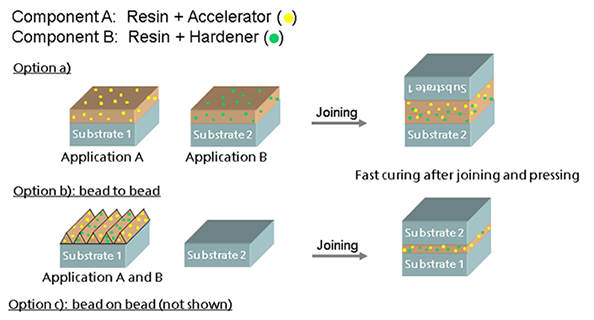
A/B method
- Aim: Simplification of the processing due to easily manageable 1:1 mixtures instead of mixing ratios that are difficult to achieve (e.g. 100:3); pot life not relevant
- Principle: Use of two components A and B in a 1:1 ratio, either separately applied to the substrates (in this case they only react with each other on joining (pressing together) the substrates) or admixed prior to application
- Application: Application of component A on substrate A and component B on substrate B; or machine application of the two components on top of each other or next to each other on substrate A; or application of the mixture
- Component A: MMA monomer and accelerator, can usually be stored for ca. 6 months
- Component B: MMA monomer and adequate hardener for the total mixture (A+B). Can be stored for ca. 6 months.
No-mix method
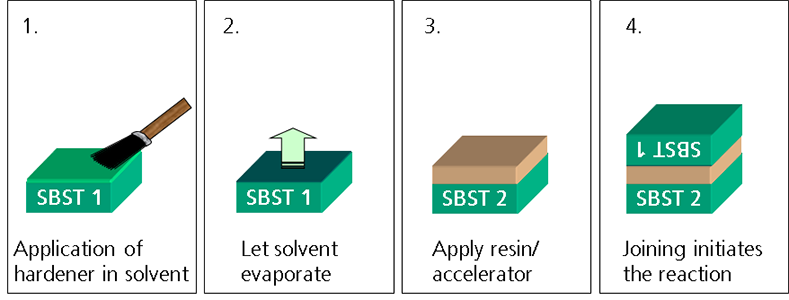
No-mix method
- Aim: Simplification of the processing by eliminating mixing steps; pot life not relevant
- Principle: Application of the hardener as a hardener-lacquer on substrate A, application of the resin and accelerator on substrate B, reaction and curing after joining
- Hardener-lacquer: Solution of the hardener in a highly volatile solvent
- Processing: After application of the hardener-lacquer (e.g. using a spray or brush) and a short evaporation phase, the substrate can in some cases be stored for several weeks; maximum film thickness 0.3 – 0.4 mm due to the fact that the polymerisation progresses on just one side
Typical properties of the cured adhesives:
- High strength
- Relatively flexible, medium elongation at fracture
- Temperature for continuous use: up to 100 °C, short periods up to 180 °C
Points to heed:
- Heed the mixing ratio
- Do not mix the accelerator and hardener: risk of explosion!
If you have questions about the product then see the technical data sheet or contact the adhesive manufacturer
Polymerisation adhesives: Anaerobically curing adhesives
General description:
- One-component adhesives (1-C)
- Cure in the absence of oxygen on metal contact (copper or iron)
- Cure to become thermosets
Physical properties of the non-cured adhesive:
- Liquid
Processing properties:
- Manual, semi-automated or fully automated processing
- For preferred equipment contact the adhesive manufacturer
- Processing temperature: room temperature
- Normal contact pressure
- 1-C processing
- Curing on metal contact (copper or iron) in the absence of oxygen
- Adhesive film thickness: 0.02 – 0.3 mm
- Geometry must guarantee oxygen exclusion (e.g. hub-shaft connections, bolts)
- Active surfaces provide the required metal ions; for passive surfaces (plastics, stainless steel) use an activator
- Final strength after 3 to 24 hours
- Secure until the bonded joint has reached hand strength
- Take relevant measures for health and safety at work and environmental protection (General: see Section 7; Details: see safety data sheet)
Typical properties of the cured adhesives:
- Various adhesive systems of differing strength (low, medium, high), depending on requirements
- Temperature for continuous use: -60 °C to max. 150 °C, short periods up to 180 °C
- High resistance to impacts and vibrations
- Very good resistance to oil, solvents and moisture
- High strength systems can only be detached at temperatures of 300 – 400 °C
Points to heed:
- Guarantee oxygen exclusion by selecting a suitable geometry
- Ensure metal contact or use an activator
If you have questions about the product then see the technical data sheet or contact the adhesive manufacturer
Polymerisation adhesives: Radiation curing acrylates
General description:
- 1-C processing
- Curing via light of a specific wavelength; usually UV light
- Cure to become thermoplastics; in a few cases thermosets
Physical properties of the non-cured adhesive:
- Liquid
Processing properties:
- Manual, semi-automated or fully automated processing
- For preferred equipment contact the adhesive manufacturer
- Processing temperature: room temperature
- Normal contact pressure
- Curing via light of a specific wavelength; usually UV light
- Light is required throughout the curing process
- Adhesive film thickness: 0.1 – 0.5 mm
- Heed the light dose; over-curing is not possible but degradation reactions can occur on far exceeding the optimum dose
- Curing time: between 1 s and several minutes
- At least 1 substrate must be transparent to the radiation
- Secure until the bonded joint has reached hand strength
- Take relevant measures for health and safety at work and environmental protection (General: see Section 7; Details: see safety data sheet)
Typical properties of the cured adhesives:
- Medium to high strength
- Varying flexibility depending on the raw material
- Relatively high impact resistance
- Temperature for continuous use: -30 °C to ca. 120 °C, higher for short periods
- For some applications (e.g. bonding glass) post-curing using sunlight
Points to heed:
- At least one substrate must be transparent to the radiation required for curing
- Radiation dose depends on a number of factors, e.g. adhesive product, adhesive film thickness, substrate material and thickness, radiation source and the distance between the radiation source and adhesive film
If you have questions about the product then see the technical data sheet or contact the adhesive manufacturer
Polymerisation adhesives: Light activated epoxides
General description:
- 1-C processing
- Curing via light of a specific wavelength; usually UV light
- Cure to become thermosets
Physical properties of the non-cured adhesive:
- Liquid
Processing properties:
- Manual, semi-automated or fully automated processing
- For preferred equipment contact the adhesive manufacturer
- Processing temperature: room temperature
- Normal contact pressure
- Adhesive film thickness: 0.1 – 0.5 mm
- Curing via light of a specific wavelength; usually UV light
- Course of the curing: 3 – 60 s light exposure (light activation), then up to 24 h curing without exposure (dark reation)
- Acceleration and higher strength via heat-aided curing; in some cases post-curing required
- Heed the light dose
- Bonding of light-permeable substrates: Light activation and dark reation in the bonding area
- Bonding of light-impermeable substrates: Light activation prior to joining; Dark reaction after joining
- Secure until the bonded joint has reached hand strength
- Take relevant measures for health and safety at work and environmental protection (General: see Section 7; Details: see safety data sheet)
Typical properties of the cured adhesives:
- High strength
- Brittle, low elongation at fracture
- Temperature for continuous use: -30 °C to max. 120 °C, short periods up to 180°C
- Very good resistance to oil, solvents and moisture
Points to heed:
- Heed the light dose
- Light dose depends on the adhesive product, light source and the distance between the light source and adhesive film
If you have questions about the product then see the technical data sheet or contact the adhesive manufacturer
Polymerisation adhesives: Unsaturated polyesters
General description:
- Two-component adhesives (2-C)
- Resin contains styrene (solvent); this partially evaporates during curing
- Cure to become thermosets
Physical properties of the non-cured adhesive:
- Consistency: Liquid to paste-like
Processing:
- Manual, semi-automated or fully automated processing
- For preferred equipment contact the adhesive manufacturer
- Processing temperature: room temperature
- Normal contact pressure
- Adhesive film thickness: 0.2 – 0.5 mm
- 2-C processing
- Room temperature curing with a catalyst or hot curing in an oven
- Alter the curing by varying the amounts of added accelerator and inhibitor
- Relatively high shrinkage on curing
- Secure until reaching hand strength and during the entire oven process
- Take relevant measures for health and safety at work and environmental protection (General: see Section 7; Details: see safety data sheet)
Typical properties of the cured adhesives:
- High strength
- Relatively flexible (less than PUR)
- Maximum temperature for continuous use up to ca. 140 °C
- High fatigue strength
Points to heed:
- Heed the mixing ratio
- Thorough mixing absolutely essential, but avoid the incorporation of air bubbles
- The processing time / pot time depend on the ambient temperature, quantity of mixture and the particular adhesive product
- Once the pot time has lapsed, do not use any more of the adhesive and dispose of any unused adhesive in the proper way!
- Once the processing time has lapsed, the position of the bonded substrates may not be further altered
- Check the thermal stability of the substrates prior to curing (in an oven)
- Take into account the heating-up time and cooling-down time for the substrates; this time must be added to the curing time for the adhesive
→ Take special care with thick substrates - The heating temperature refers to the temperature in the joint
→ Take special care with thick substrates - Stress can develop in the joint on heating and cooling
If you have questions about the product then see the technical data sheet or contact the adhesive manufacturer