6.7 Long-term stability
The longer a bonded joint can
- …. withstand chemical, physical and biological loads …
- … in combination with mechanical loads, …
- … without undergoing unacceptable changes to key quality-determining properties (in particular: strength, deformation properties)…
the more resistant the bonded joint!
Prediction of ageing
Only in rare cases is the cause of ageing a single factor. Usually several factors act simultaneously, namely their effects overlap.
The overall effect is not simply the sum of the effects of the individual factors. Rather, there are complex interactions and these can lead to several-fold amplification and in other cases to diminution of the effects.
As the future influences on a bonded joint are usually not known in advance, but can merely be estimated, exact prediction of the course of ageing is not possible. → Estimation of real ageing based on ageing tests and practical experience in the field
Estimation of the long-term stability
Often required: A service life of 20 years or more.
For high-performance adhesives which have only been developed in recent years, practical and experimental experience about such long timescales is not available.
Nevertheless, adhesive manufacturers, adhesive users and independent advisors can in many instances draw on existing experience with similar adhesive systems. Procedures for artificial (accelerated) ageing are, however, necessary.
In order to study ageing behaviour within a reasonable experimental time frame, bonded joints are subjected…
- … over short periods …
- … to elevated loads/stresses (temperature, relative humidity, concentration) …
- … → “time-lapse” effect
DIN EN ISO 9142: Adhesives, guidelines for selecting laboratory ageing conditions for testing bonded joints
- Definition of preferred temperatures, test duration and relative humidity
- Proposed ageing cycles which variously comprise heat, cold, water and salt water in different combinations
Many companies use company-specific procedures for practical estimation of the ageing behaviour.
Key requirements for laboratory ageing procedures
- Artificial ageing in the laboratory should if possible cover all relevant combinations of loads/stresses.
- The maximum possible “time-lapse” effect should be aimed for, under realistic conditions. Note! Too extreme values (e. g. in the choice of temperature or the concentration of the media) can result in changes which do not occur in practice!
Programmable climate test cabinets:
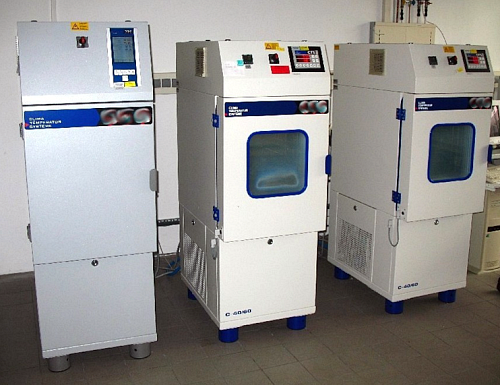
Accelerated ageing (examples)
1) Constant climates
- Storage under constant climatic conditions (combination of temperature and relative humidity) over a longer period
- Adapted to the area of usage
Examples:
- Variant 85 / 85 (→ 85 °C / 85% rel. humidity), standard in the microelectronics industry, duration: 2000 hours
- Condensation test (DIN EN ISO 6270): 40 °C, 100% rel. humidity, duration can be selected (e.g. car manufacturing industry: 1000 hours)
2) Alternating climate tests (DIN EN ISO 9142)
- Exposure to two or more sets of climatic conditions in cycles
- Specified holding times and transition times
→ e. g. simulation of outdoor weathering (day/night or summer/winter)
Example: Study the effect of temperature and humidity changes outdoors
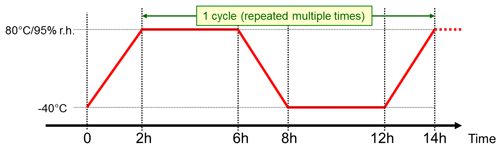
3) Salt-spray test (DIN EN ISO 9227)
- Spray the test specimen in a chamber with 5% NaCl solution for a specific period (usually 1000 hours)
- Mechanical testing at 35 °C
- In general this is combined with other ageing procedures (e.g. the alternating climate test)
→ Acceleration of corrosion (bonded metal joints!)
e. g. as part of the “VDA alternating test” (see: Combined ageing and testing)
4) Cataplasma test (DIN EN ISO 9142; Annex E2)
-
- The test specimen (e.g. lap shear speciemen) is wrapped in water-soaked cotton-wool and sometimes aluminium foil and then sealed air-tight in PE film
Storage for a longer period at elevated temperatures, followed by rapid cooling to below the freezing point (e.g. 2 weeks at 70 °C followed by rapid relocation (max. 30 min); After being unwrapped, the test specimens are stored for 2 hours at -20 °C; After subsequent reconditioning under the standard climate, the testing is carried out)
Specimens in a closed atmosphere → Corrosion products are not transported away and can act further on the bonded joint; No drying prior to cooling → Frost damage
5) Effect of exposure to light/UV radiation:
- DIN EN ISO 4892-1, -2, -3: Plastics; Artificial exposure to radiation or weathering in test chambers
6) Effect of exposure to contaminants and media:
- DIN EN ISO 175: Plastics; Method for determining the effect of liquid chemicals by exposing the test specimens to the media for a specific duration at a specific temperature
7) Combined ageing and testing
e.g. VDA alternating test (VDA 621-415)
- 24 h salt-spray test (DIN EN ISO 9227)
- 96 h condensation test under alternating climatic conditions (DIN EN ISO 6270-2)
- 48 h storage at room temperature (18 to 28 °C)
VDA = Verband der deutschen Automobilindustrie (Association of German Car Manufacturers)
Outdoor weathering:
- Storage of bonded samples outside, e.g. on the roof
- Simultaneous effect of changing temperature, humidity, light and aggressive gases
- Recommendation: Use pre-stressed or pre-strained samples
→ Effects differ from the effects of laboratory ageing procedures
- Depend on the geographic region and weather conditions (Experience: e. g. 1 year in an extreme climatic zone (Florida: humid/hot) equals about 6 – 8 years in Central Europe; Source: VW)
- Valuable addition to laboratory results
Comparison: Artificial and real ageing
Comparison of the real ageing of components with the results of laboratory ageing experiments allows correlations to be made (time-lapse factor).
However, note:
- The acceleration of the effects is not constant over each individual time segment.
- Altered, unexpected or rarely occurring influences could accelerate ageing in the future more than expected from experience up until now → Set safety factors