8.2.3 Processing the adhesive
Use the technical data sheet as the basis for work instructions
- Processing conditions
- Processing times (pot life, skinning time, open time, etc.)
- Curing conditions
Important additional information for processing 2-C adhesives:
- Mixing ratio (weight or volume basis)
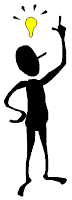
1-C processing
- Use the container size that is suitable for the expected adhesive usage
- Heed adhesive-specific processing times (skinning time, airing time / evaporation time, etc.)
2-C processing
- Heed the maximum quantity of adhesive to mix
- Heed the pot life (depends on the quantity of mixed adhesive, temperature)
- Size of the mixing container must be suitable for the quantity of adhesive (fill height ca. 1/4 to 1/2 of the container height)
- Only use containers for mixing once!
- Use suitable stirrers (reusable stirrers made of steel or glass, disposable stirrers made of wood)
- Mix very thoroughly (homogenous mixture!)
- Avoid incorporating air bubbles (this is a particular risk for high viscosityadhesives)
- Prepare samples for quality control (label beakers and allow to cure in a suitable place → quality control)
- Clean reusable stirrers with a suitable solvent
- Dispose of residues in the proper way
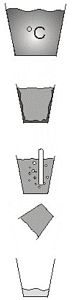
2-C adhesives are often supplied as twin cartridges which make manual mixing unnecessary. This is preferred because it eliminates weighing and mixing errors. It is however important here to follow the manufacturer’s instructions.

Mixing ratio
Indicated on the technical data sheet for the adhesive as parts by volume (VA:VB) or parts by weight (mA:mB)
Interconversion using the density (=specific weight) ρ:
Twin cartridge with a suitable delivery gun
The cross-section ratio of the two pistons determines the mixing ratio (e. g. 1:1, 2:1, 4:1, 10:1)
Different sizes (e. g. 50 ml, 200 ml, 400 ml)
Static mixer provides homogenous mixing
→ No errors regarding the mixing ratio or quality of mixing
Do not use the first few centimetres of adhesive coming out of the mixer nozzle (rule of thumb: ca. one mixer length)!
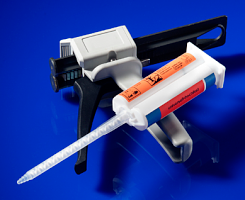
Source: Fraunhofer IFAM
In order to ensure that the mixing ratio is correct from the start, the delivery gun should be activated, before positioning the mixer on the cartridges, until material emerges from both chambers; only then are the two pistons at the same height.
The delivery gun must be undamaged and in particular the piston rods must not be bent. Otherwise the mixing ratio may not be correct.
- To clean metal and glass stirring rods: use the appropriate cleaning agent and fluff-free cloths. Wooden spatulas must be thrown away.
- It is best to leave unused adhesive to harden in the application vessel; it can be used as a test sample for monitoring the curing properties.
- Cleaning cloths contaminated with non-cured adhesive must be disposed of as waste requiring special control (previously: hazardous waste).
- Resin or hardener components that are no longer required must be collected in a suitable sealable container and if necessary disposed of as waste requiring special control (previously: hazardous waste).
- Stirring rods and spatulas used for weighing out materials must be thoroughly cleaned with a cloth and solvent in between weighing out the resinand weighing out the hardener. No resin residues must end up in the container of hardener (and vice-versa).
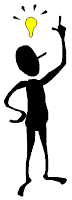