7.3 Process steps in the production phase
Specific quality assurance measures in the production phase
1. Logistics (transport, goods receipt, storage, availability of special materials, disposal)
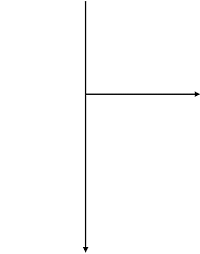
- Dispatch tests and test certificate of the manufacturer
- Monitor transport
- Check and test materials (identity, appearance, rheology, composition, usability, expiry date)
- Labelling of containers (date of receipt)
- Samples
- Monitor storage conditions (temperature, humidity, time, light intensity/ radiation)
- Availability of special materials (e.g. tape for marking areas off, warning signs, “wet adhesive” stickers, silicone-free skin-cleaning and skin-care products)
- Ban sources of contamination (e.g. silicones; also from gloves, cleaning cloths, lubricants, cleaning and impregnating agents, etc.)
- Optimise organisational systems (e.g. for storage)
- Heed specifications
- …
2. Ensure optimum ambient conditions
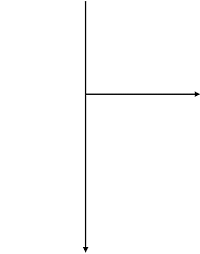
- Mark off the area where work is to be carried out and ensure unauthorised persons do not enter the work area
- Protect the work area from contamination via the air
- Take measurements in the work area (temperature, humidity, dust, aerosols, gases, light intensity)
- Avoid draughts
- …
3. Acclimatise the substrates, primer and adhesives
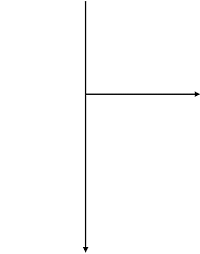
- Definition of location, temperature, time and tolerances
- Measurements (ambient temperature, surface temperature, time)
- …
4. Test the accuracy of fit
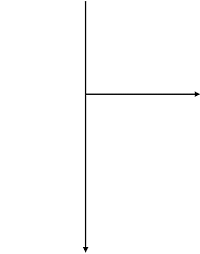
- Check the accuracy of fit and tolerances using suitable test and measurement methods (e.g. templates)
- Check substrates for other damage and abnormalities
- …
5. Cleaning
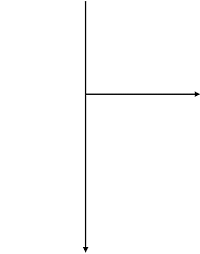
- Thoroughly rinse off aggressive cleaning agents
- Avoid recontamination (e.g. via contaminated cleaning agents, cloths, gloves)
- Prepare a summary of the dependence of the evaporation time on temperature and humidity
- When using adhesive tape for masking purposes bear in mind that residues may remain after removing the tape
- Measurements (time, pressure, temperature, composition, surface contamination)
- Monitor (settings, appearance)
- Associated tests (e.g. wetting tests with test inks, contact angle method))
- Labelling of containers
- Minimise storage and transport times after cleaning
- Monitor storage and transport conditions after cleaning
- …
6. Pretreat surfaces
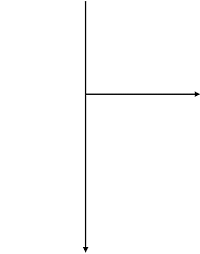
- Never pretreat contaminated surfaces without cleaning them adequately
- Only use contamination-free materials (e.g. etching agents, grit for blasting, sandpaper)
- Thoroughly rinse off any aggressive pretreatment agents (e.g. etchingagent)
- Measurements (time, pressure, temperature, stress, composition, layer thickness, degree of coverage)
- Monitor (settings, appearance)
- Associated tests (e.g. wetting tests with test inks, contact anglemethod)
- Labelling of containers
- Minimise storage and transport times after pretreatment
- Monitor storage and transport conditions
- …
7. Primers (also applies for activators, pre-applied activators, etc.)
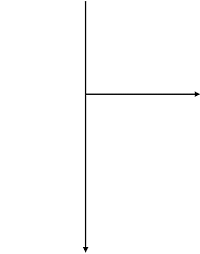
- Strict protection of primers from contamination and moisture, reseal containers immediately
- Use coloured materials
- Apply the correct layer thickness, avoid applying excess
- Prepare a summary of the dependence of the drying time on temperature and humidity
- Measurements (layer thickness, degree of coverage)
- Monitor (appearance, rhelogy)
- Labelling of containers (e.g. date of first opening, shelf-life after first opening)
- Minimise storage and transport times after priming
- Monitor storage and transport conditions
- Monitor storage and transport times
- …
8. Adhesive stocks
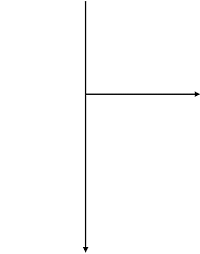
- Protect adhesive from contamination and moisture, reseal containersimmediately
- Use coloured adhesives
- Measurements (temperature, pressure, time, contamination, thorough mixing, rheology, usability)
- Monitor (settings, appearance, air contact)
- Labelling of containers (e.g. date of first opening, shelf-life after first opening)
- Monitor storage and transport conditions
- Monitor storage and transport times
- …
9. Feeding
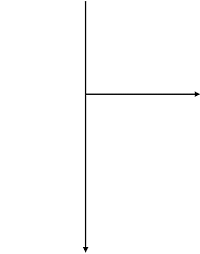
- Protect the adhesive from contamination (e.g. use water-impermeable tubing)
- Measurements (temperature, pressure, volume, weight, time, rheology)
- Monitor (settings)
- …
10. Dosing
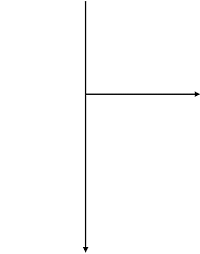
- Twin cartridge for manual processing; for automatic processing use 2-C dosing and mixing unit
- Automatic control circuit sensor-machine
- Measurements (pressure, volume, weight, time)
- Monitor (settings)
- …
11. Mixing
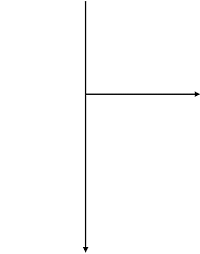
-
- Use coloured components
- For small quantities, twin-cartridge with static mixer or use 2-C adhesives premixed by the manufacturer and stored under cool conditions
mixing ratio
- Check the quality of mixing
- Stipulate the rinsing interval, maintenance interval, change interval for dynamic mixers
- Measurements (progress of the curing, usability, rheology, time)
- Monitor (settings, appearance)
- …
12. Application
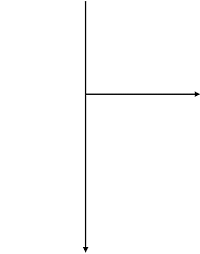
- Definition of quantity to be applied, application pattern and geometry of the bonding area
- Ensure the correct film thickness is applied, especially for solvent-containing contact adhesives
- Avoid closed voids which could cause condensation of moisture
- Stipulate the maximum processing time
- Stipulate the minimumbcuring time
- Use coloured / fluorescing adhesives
- Automatic control circuit sensor-machine
- Measurements (quantity, position, shape, contamination)
- Monitor (position, shape)
- Associated tests (e.g. wetting tests, bead peel test)
- …
13. Joining the substrates
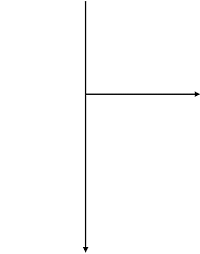
- Keep the adhesive film thickness within the prescribed tolerance
- Avoid closed voids where moisture could condense
- Automatic control circuit sensor-machine
- Measurements (width, thickness, tolerances, pressure)
- Visual inspection
- …
14. Fixing
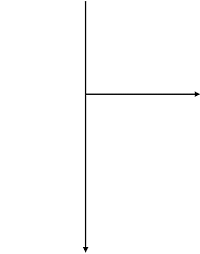
- Avoid non-permitted stress during and after fixing
- Automatic control circuit sensor-machine
- Measurements (tolerances, pressure)
- Visual inspection
- …
15. Curing
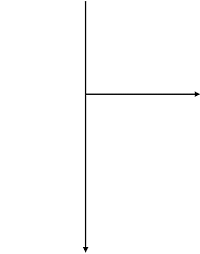
- Protect from unpermitted loads/stresses during the curing process
- Prepare summary of the dependence of the curing process on humidity, temperature, pressure and dose
- Avoid build up of high stress in the bonded joint by optimising the curing parameters
- Stipulate the strength required for handling
- For hot-curing adhesives ensure the curing temperature in the joint is reached for the necessary time
- Automatic control circuit sensor-machine
- Measurements (temperature, humidity, dose, time, pressure)
- Monitor (settings)
- Associated tests (e.g. bead peel test)
- Samples
- Final checks:
- Work samples or random samples: destructive tests to demonstrate that the required and geometry have been achieved strength Random samples or 100%-test: non-destructive tests to demonstrate that the required geometry has been achieved
- …