7.4 Health and safety at work and environmental protection
Most adhesives and auxiliary materials such as primers, activators, cleaning agents, etc. are classed as hazardous substances, namely they have a certain hazard potential and require special storage, transport, processing and disposal.
Health and safety at work and environmental protection are important when working with these materials and relevant measures must be taken into account in the production planning.
The following pages introduce important aspects of health and safety at work. Particular matters relating to specific workplaces cannot however be covered here. These can however be evaluated in consultation with external advisers or by the company safety officer in some cases. A key source of information is the safety data sheet of the product. This is provided free-of-charge by the manufacturer and is delivered with the product.
Hazardous substances used in adhesive bonding work
- Adhesives
- Substances used during the surface treatment, for example:
- Primers
- Etching solutions
- Cleaning agents
- Gases (flame treatment, plasma treatment)
- Substances formed during subsequent processes, for example:
- Gases released during spot welding
- Reaction products of subsequent processing steps
Employers must guarantee the health and safety of employees in the workplace (a duty to safeguard their employees) and have a duty to provide employees with information (prepare work instructions, make safety data sheets available, annual instruction and if necessary medical advice)
Obligations of employees (selection):
- Not to endanger oneself or others
- To use the personal protection equipment which is made available
- To report risks and shortcomings with equipment, plants, etc.
- To follow the instructions of the employer
Examples of hazardous substances in bonding processes:
- Adhesives (that are not fully cured/hardened)
- Primers / activators
- Cleaning agents
- Etching solutions
Labelling of hazardous materials
- Name of the material or
- trade name for formulations (with indication of hazardous substances)
- Hazard symbols and hazard descriptions
- Risk statements (R-statements)
- Safety recommendations (S-statements)
- Name, address and phone number of the supplier
- EU number (if available)
- Quantity in the container
Label design
- Durable and in the German language
- Commensurate with the size of the packaging
- Placed on one or several sides of the packaging
In-company labels
- All substances used at the workplace must be able to be identified.
- Hazardous materials must also be labelled with hazard symbols and hazard descriptions.
- All equipment and tubes/hoses containing hazardous materials must also be labelled.
- The containers must be suitable for the purpose.
- The containers must not be able to be confused with containers for foods.
Globally harmonised system
As the trade in and use of hazardous materials have become ever more global, efforts have been made over a long period to harmonise the various national systems.
GHS/ CLP hazard symbols
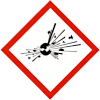
- Explosive substances and mixtures and products containing explosive substances
- Some self-decomposing substances and mixtures
- Some organic peroxides
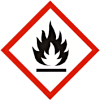
- Flammable gases, gases, aerosols, liquids and solids
- Some self-decomposing substances and mixtures
- Pyrophoric liquids and solids
- Self-heating substances and mixtures
- Substances and mixtures which liberate flammable gases in contact with water
- Some organic peroxides
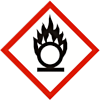
- Flammable (oxidising) gases, liquids and solids
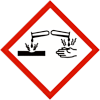
Substances and mixtures
- which cause irreversible damage to the skin or eyes
- which are corrosive to metals
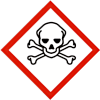
- Substances and mixtures with a lethal or toxic effect (acute toxicity)
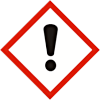
Substances and mixtures
- which are harmful to health
- which cause reversible damage to the skin or eyes
- which can trigger an allergic reaction on skin contact
- which irritate the respiratory tract or have a narcotic effect
- which damage the ozone layer
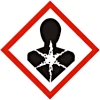
Substances and mixtures
- which cause hypersensitivity of the respiratory tract
- which are carcinogenic, mutagenic or toxic for reproduction or are suspected of having such effects
- which cause specific organ damage after one-off or repeated exposure
- which can be fatal on penetration into the trachea or lower respiratory tract (aspiration hazard)
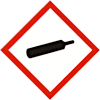
- Gases under pressure
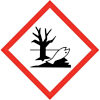
- Substances and mixtures which cause acute and/or longer term harmful effects to water organisms
Without
pictogram
- Some substances and mixtures which are harmful to water organisms
- Substances which can harm newborns via breast milk
- Some flammable gases
Uptake routes for chemicals into the human body
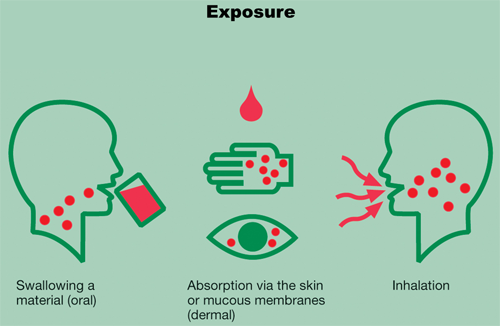
Protective measures
Priority of measures
- Eliminate the risk (e.g. use another substance instead of the hazardous material)
- Technical measures (e.g. encapsulation, extraction)
- Organisational measures (e.g. time-exposure limit, instructions)
- Personal protection equipment (e.g. gloves, mask for breathing protection, safety glasses)
Measure 1 must be tried first of all, without considering the cost. This must be documented. Personal protection equipment (measure 4) is the last measure for protection. Measures 2 and 3 must be fulfilled, but there is more versatility here regarding the sequence.
Personal protection equipment (PPE)
- PPE covers all equipment to be used or worn by employees in order to protect them whilst carrying out their work.
- PPE is the protective measure of last resort.
- PPE must be chosen and made available by the employer and used by the employees.
- PPE must be suitable for the purpose.
- Information can be obtained from the safety data sheet and the work instructions.
Personal protection equipment (examples)

Eye protection

Breathing protection

Ear protection

Head protection

Hand protection

Body protection

Foot protection

Hand protection
- Protective gloves must provide protection for the hands from harm due to external effects of a mechanical, chemical and thermal nature, and must protect the hands against microorganisms and ionising radiation
- Gloves may not be worn when working with machinery with rotating parts (e.g. circular saws, drills, etc.).
- Instructions for use must be prepared to ensure the correct use of protective gloves.
- Information about suitable gloves can be obtained from the safety data sheet.
- Gloves providing protection against chemicals must prevent the relevant chemicals reaching the skin.
- Such gloves are almost exclusively made of plastic.
- The materials from which the gloves are made can cause allergies.
- The protection time indicates how long there is protection against a certain substance permeating through the material.
- This time depends on the substance, its concentration and the material used to make the gloves.
Employees require information about how to work with hazardous substances.
A distinction must be made here between the safety data sheet and the instructions for use. A further source of information is the label on the packaging which also contains important information.
The employer must also provide annual instruction.
Sources of information about health and safety at work
- Instructions for use / work instructions
- Prepared by the employer
- Specific for the workplace and tasks
- Must be available at the workplace
- Safety data sheet
- Must be made available free of charge by the manufacturer
- Very detailed, also contains information about storage and transport
- Specific for the product
- Packaging (label)
Disposal
The first priority is to prevent unnecessary waste, and especially waste requiring special control (previously: hazardous waste). If this is not possible, the following points must be taken into account for disposal:
Typical regulations for disposal
- Non cured/hardened adhesives and other hazardous substances are waste materials requiring special control (previously: hazardous waste).
- Waste materials requiring special control (previously: hazardous waste) may not enter drains or be mixed with the “normal” industrial waste.
- Fully cured/hardened adhesives are plastics and can be disposed of as normal industrial waste.
Product-specific information can be obtained from the safety data sheet.
If necessary the user should contact the waste disposal company and include the adhesives or other materials being used in the disposal plan of the company. In principle, materials should be disposed of following the disposal instructions on the safety data sheet.